工場では生産性の指標となるのが設備の稼働率です。稼働率は工場の売上につながるので、100%に近い数字をキープするのが理想ですが、現実的になかなかそう上手くはいかないものでしょう。
管理監督者のみならず、一般作業者も稼働率は意識しないと生産性は向上しないといえます。そこで、工場の稼働率の考え方や内訳、向上させるポイントなどを解説していきます。
工場の稼働率とは
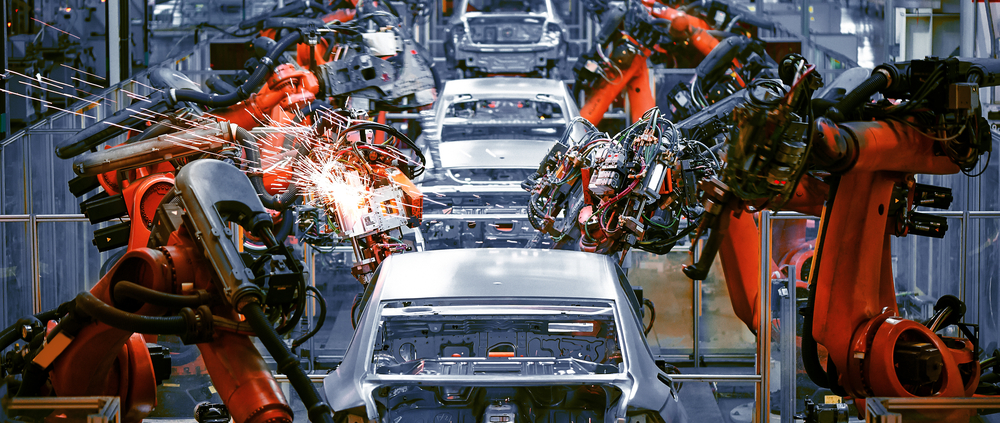
工場の稼働率は主に作業時間と設備のサイクルタイム(速度)に分けて考えます。早い話が時間をフルに使って、加工速度を上げると稼働率が向上するものです。ただ、その通りにいかないのが現実であり、ムダな作業や時間を省くことで生産性を上げていくように考えます。
そこで、まずは稼働率の内訳(時間と速度)をみていきましょう。
時間性稼働率
時間性稼働率(時間稼働率)は1日の作業時間に対して、どの程度有効に設備が稼働していたかを算出します。
たとえば1直の総労働時間を480分(8時間)として、作業できた時間が420分(7時間)だったと仮定します。420÷480=0.875となり、時間稼働率は87.5%となるのです。
動いていない60分はダウンタイムに換算されます。
時間稼働率=実作業時間 ÷ 総労働時間
ただ、実作業時間というのはストップウォッチを常に持ち歩いている訳ではないので、作業していた時間というのはなかなか分かりません。トイレや水分補給、ミーティングや掃除、片付けなどで設備は必ず止まる時間があります。そこで、実作業時間を別の形で算出する方法が必要となります。
この時間稼働率の実作業時間の算出方法は、設備のサイクルタイムに影響します。製品1つ当たりにかかる加工時間がサイクルタイムなので、仮に30秒で1つ加工される製品の場合、時間稼働率が100%とすると、1時間当たり120個の生産個数になります。
この生産個数から実作業時間が判別できるようになり、時間稼働率の算出が可能となるのです。
・1個当たりのサイクルタイム 30秒(1分で2個の生産個数)
・1時間当たりの理想生産個数 120個
・1直の生産個数 840個
・1直当たりの理想生産個数 960個
・時間稼働率 840÷960=0.875(87.5%)
1直の生産個数が840個と分かって、初めて実作業時間が420分(7時間)であることが判明します。
時間稼働率が何%以上で優秀というのは、業種や作業形態によって異なりますが、100%に近いほうがベストであることは間違いありません。
時間稼働率が低いということは、それだけ設備が停止している時間が長いという意味を成しています。
速度性稼働率
速度性稼働率(速度稼働率)は設備が本来持っている100%の能力を発揮したときの標準サイクルタイムをベースとして算出します。本来の標準サイクルタイムが30秒のとき、現状の稼働サイクルが30秒だと100%となり、35秒だと85.7%、25秒だと120%の速度稼働率となります。
速度稼働率= 本来の標準サイクルタイム÷ 現状のサイクルタイム
速度稼働率が上がれば、同じ時間稼働率でも生産本数は向上します。たとえば先述した420分(7時間)ベースで、本来の標準サイクルタイムが30秒のとき、現状の稼働サイクルが25秒・30秒・35秒の場合を考えてみましょう。
表1:標準サイクルタイム30秒で設定した場合の生産個数と稼働率
|
1時間の生産数 |
7時間の生産数 |
時間稼働率 |
速度稼働率 |
25秒 |
144個 |
1,008個 |
87.5% |
120% |
30秒 |
120個 |
840個 |
87.5% |
100% |
35秒 |
103個 |
721個 |
87.5% |
87.5% |
ご覧のように同じ時間稼働率でも、速度稼働率に違いがあれば生産数も大幅に変化します。
このことからも速度稼働率を向上させることは、生産数性向上につながることが分かります。
設備の有効稼働率を算出
次に設備が如何に有効稼働しているかを算出する方法を紹介します。
これは有効稼働率ともいいますが、工場によって呼び名が変わっている場合があります。時間稼働率と速度稼働率を掛け合わせることで算出でき、どちらかが悪いと工場内の設備が有効稼働していません。
有効稼働率= 時間稼働率× 速度稼働率
上記の速度稼働率の表で設備がどれだけ有効稼働していたのか割合をみていきましょう。
表2:標準サイクルタイム30秒で設定した場合の生産個数と有効稼働率
|
1時間の生産数 |
7時間の生産数 |
時間稼働率 |
速度稼働率 |
有効稼働率 |
25秒 |
144個 |
1,008個 |
87.5% |
120% |
105% |
30秒 |
120個 |
840個 |
87.5% |
100% |
87.5% |
35秒 |
103個 |
721個 |
87.5% |
87.5% |
76.6% |
この表ではサイクルタイムが35秒のとき、時間稼働率と速度稼働率が共に87.5%となっているのに対し、有効稼働率は76.6%と10ポイント以上も減少しているのが分かります。
このような場合には、時間にも速度にもムダがあるというので改善が必要です。
稼働率の改善で生産性向上を担う
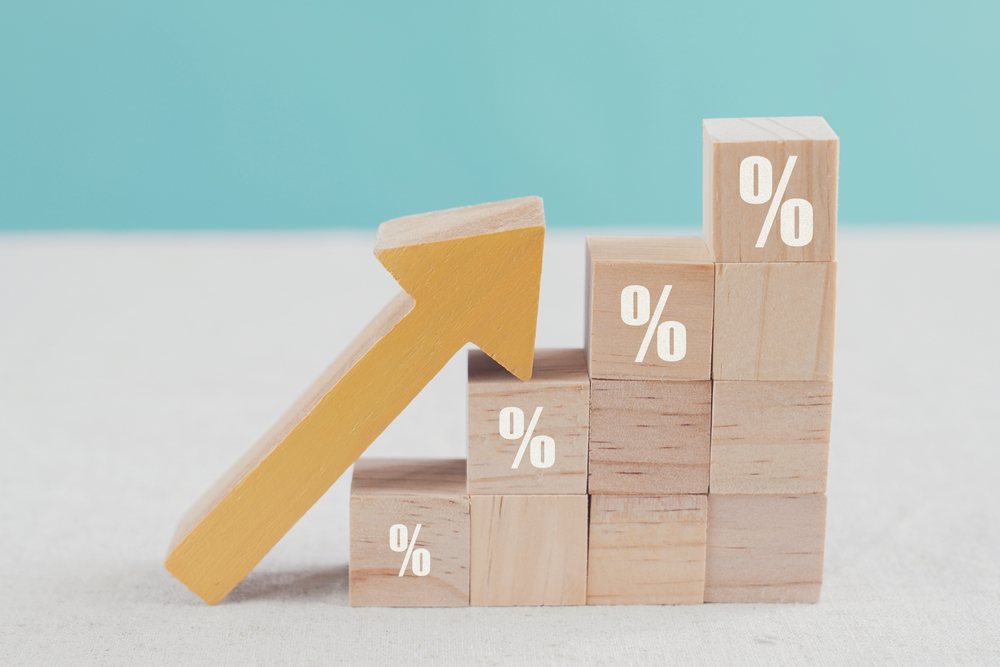
稼働率が低い場合は改善を行うことで生産性を高められます。
どのような改善方法があるのかみていきましょう。
時間稼働率が低い場合
時間稼働率は設備が停止している時間を指しています。停止している時間はダウンタイムとして計上しますが、まずはどのようなダウンタイムがあるのか、しっかりとリサーチするところから始めないといけません。
表3:設備停止の要因
会議や打ち合わせなど |
朝礼やミーティング、会議、訓示、QCサークル、KYTなど |
稼働中のチョコ停 |
段取りミスや部品劣化・摩耗による動作不良など |
段取り |
設備段取り替えに関わる時間 |
材料待ち |
前工程待ちが発する時間 |
設備トラブル |
設備の故障や漏電など稼働できない状態 |
人待ち |
体調不良など突発的な休暇による人手待ち |
もちろん、これら以外にも見えない待ち時間が発生するものです。日報を記入する時間やトイレ、水分補給、清掃、運搬などがあります。
ミーティングもついダラダラしてしまうと時間がかかってしまいます。時間を決めてすぐに生産体制に入れるようにすることも大切です。
また、段取りは業種によって経験がモノをいうはずですから、時間をかけてでもしっかりと教え込む姿勢も大切ですし、チョコ停が出ないようにしないといけません。動作不良などでチョコ停が発生する場合、時間稼働率も下がりますが、不良品が流出するような品質トラブルの恐れがあります。
まずはこれらのダウンタイムを抽出し、どのような課題があるのか調べておき、対策を考えるようにしましょう。
速度稼働率が低い場合
速度稼働率が低い工場や生産ラインはサイクルタイムが遅い傾向にあります。設備導入時の標準サイクルタイムから実測の加工時間がどれだけ遅いのか調査しなければなりません。設備導入時の標準サイクルタイムは基本的に速く設定されているものです。
機械メーカーのテスト段階ではどれだけ速く加工できるかを検証しますが、実際に現場で加工する場合、製品のサイズや材質に取り代、品質精度によって大きく変化するものです。実際に速度稼働率の基準となるサイクルタイムが速過ぎないか検証することも大切です。
速度稼働率はサイクルタイムを上げるよりかは、アイドルタイムを削減するほうが効果的でしょう。
アイドルタイムは加工していない時間で、たとえば搬送時間などが挙げられます。シリンダーで製品を運ぶ場合、シリンダーの速度や待機時間など、短縮できる部分は改善するようにしましょう。もちろん、速度を上げることによってキズが発生するなど、品質に関わる部分で触るのはNGといえます。
職場の見える化を図る
工場の稼働率が悪い要因として、見える化ができていないことも挙げられます。現場の管理部門では人の動きを把握できていないと、稼働率が悪い要因を調査することもできません。複数の設備に対して作業者がどのような動線を描いているのか、作業分析がしっかりとできていないことがあります。
このような工場では、作業者も人手不足などでとにかく設備を止めないように必死になっているものの、稼働率が上がらず残業や休日出勤が増えてしまい、モチベーションも低下していく傾向になります。
また、職場の見える化を進めていくと、工場全体のムダも把握できるようになっていきます。必要な作業の合間にムダな作業が入っている場合、それが時間稼働率を下げる要因にもつながっているでしょう。
改善でムダを取り除いて稼働率を向上する
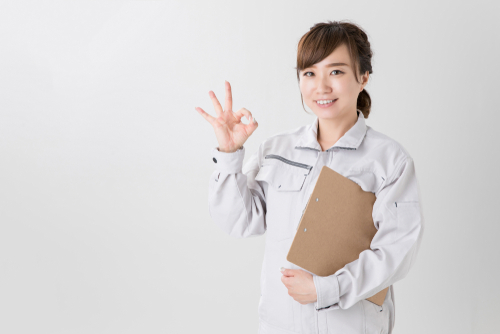
工場の稼働率を見える化にすることでムダな作業がみえていきます。どのようなムダがあるのかみていきましょう。
時間稼働率におけるムダの改善
時間稼働率には作業性のムダや配置のムダ、置き場のムダが主にあります。見える化を図ることで作業分析もしやすくなり、人の動きが分かるようになっていきます。作業者のムダな動きが分かるようになり、歩数と設備待機時間に作業性が悪く感じられ、適切な作業動線を敷くようにできます。
また、レイアウトによる人の配置にもムダがある場合、適切な人材配置をすることで改善可能です。見える化ができていない頃には1人でできる作業に2人をかけていたりすることもあれば、時間を空けてお互いが交互に回れば解決できる問題もあります。
さらに置き場にムダがある場合、段取り者が部品や治具を取りに行く時間がかかり過ぎてムダなこともあるでしょう。3定ができていない現場だと作業者のスペースが確保できず、無理な姿勢で作業しなければならないこともあり得ます。
他にも見える化によって材料や備品がどこにあるのか、なくなっているのか、発注をかけているのかといったところが見えてきます。作業者が二度手間になるようなことがなくなるでしょう。
速度稼働率におけるムダの改善
速度稼働率が見える化になることで、サイクルタイムが標準と比較してどれだけ長いのか判明します。設備の待機時間(アイドル時間)が長くなるとサイクルタイムも延びてしまいます。
どこの設備でアイドルタイムが長くなっているのかが分かれば、シリンダーの摩耗や劣化などが事前に判断できるようになり、動きが完全に悪くなってチョコ停が出る前に交換できます。
機械加工の工場では、設備に投入される材料の取り代の削減や統一を図ることで、サイクルタイムを削減させられます。ムダなエアカットがなくなりますし、取り代削減でもっと砥石のインターバルを延ばすことが可能です。
また、砥石のインターバルが延びれば、その分間材費のコスト削減になりますので、原低の効果も期待できるでしょう。
稼働率向上の注意点
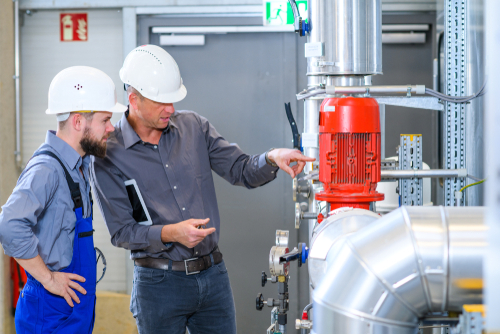
ダウンタイムを削減させて稼働率を向上させることは、生産性が上がっていいことばかり…というイメージですが、そうとも限りません。
稼働率向上における注意点を紹介していきます。
作業者の普段していることができなくなる
ダウンタイムが削減されれば、その分設備を動かしていますが、作業者が普段している作業内容ができなくなる恐れがあります。
たとえば清掃にかかる時間や日報を記入する時間、引き継ぎやミーティングにかける時間、教育をする時間など、設備が止まっている時間を無理やり動かそうとする体制を強いると、これらの時間を強制的に短縮させてしまう恐れがあるものです。
もちろん、ムダにダラダラと長い時間をかけるのは改善が必要ですが、清掃をしなくなり、日報も適当に記入し、引き継ぎや教育もほとんどない状態に陥れば、作業者の不満も高まってモチベーションが低下してしまいます。
表4:ダウンタイム削減による作業者の不満の一例
ミーティングが短い |
引き継ぎの時間が少ない |
満足に教育してもらえない |
日報記入の時間がもったいない |
掃除の時間をかけられない |
慌てて作業をしてしまう |
ダウンタイムを一方的に削減するのではなく、必要なダウンタイムはきちんと日報に落とし込み、メリハリをつけるようにしなければなりません。
サイクルタイム削減は品質トラブルの懸念
速度稼働率も同様に、サイクルタイムを上げるばかりが効率よい生産とはならないものです。サイクルタイムを上げるということは品質にも影響がでる可能性があります。一度の加工だけで判断せず、長いロットの最後まで問題ないのかなど、きちんとデータを取って作業しなくてはなりません。
研削砥石になると目詰まりを起こし、製品に焼けや精度不良などを引き起こす可能性があります。品質保証や生産技術、上長と相談の上、定められた加工条件から逸脱するようなことがあれば初回品管理をしてきっちり打ち上げるようにしましょう。
見える化によるメリット
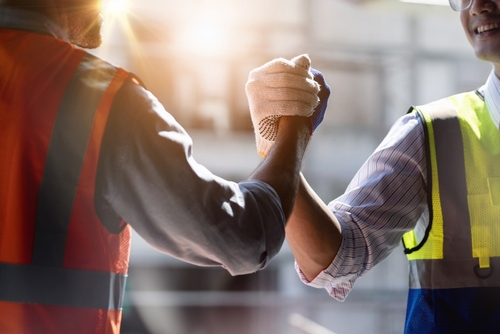
工場や職場の見える化することにより、稼働率以外にもメリットが生まれます。
1.作業者のモチベーションが上がる
2.競争意識が生まれる
3.工場の弱点が分かる
これらの内訳をみていきましょう。
作業者のモチベーションアップ
まずは作業者のモチベーションが上がりやすくなります。見える化ができていなかった職場というのは働きづらく、現場の不満も改善されなくて我慢していた人もいるはずです。現場のムダが分かるということは、作業者の困りごとの把握にもつながります。
困りごとを解決してくれるというのは、働きやすい環境でもありますので、作業者のモチベーションアップにつながるでしょう。
競争意識が生まれる
これも作業者のモチベーションにつながりますが、見える化によって稼働率もはっきりすれば、作業者にも競争意識が芽生えます。これまで生産個数であまり意識していなかった人も目に見えて結果が分かるようになればだれでも意識するものです。
険悪な関係になるのは論外ですが、作業者同士の競争意識はプロの工場勤務者としてスキルアップやキャリアアップにつながります。
工場の弱点が分かる
工場の見える化というのは、これまで見えていなかった部分が把握できることになります。職場内で見える化が工場全体に浸透することで、工場の弱点が分かるようになるでしょう。工場の弱点が分かればそこに注力することで、組織全体の底上げも可能です。生産技術や品質保証、生産管理などの部門は特に力をいれて改善に取り組むことで結果が生みやすくなります。
まとめ
稼働率には時間と速度、それらを掛け合わせた有効稼働率があり、見える化することで改善が可能です。工場の稼働率は見える化で効率化を図れますから、生産性の工場だけでなく、作業者の意識改革にもつながります。
また、稼働率を上げることだけに執着すると、作業者のモチベーションや品質の低下を生んでしまうので注意が必要です。