工場では常に順風満帆な生産活動ができるものではありません。意図しない不具合やトラブルが発生してしまう恐れがあります。
トラブルが発覚したときには、迅速な対処法が必要です。「何をすべきか」というのをしっかり理解していないといざというときに後手に回ってしまいがちです。また、常日頃からトラブルへの対策を講じることが大切といえます。
そこで、トラブルが起こる要因と対処法や対策を解説していきます。
工場で起きやすい3つのトラブル
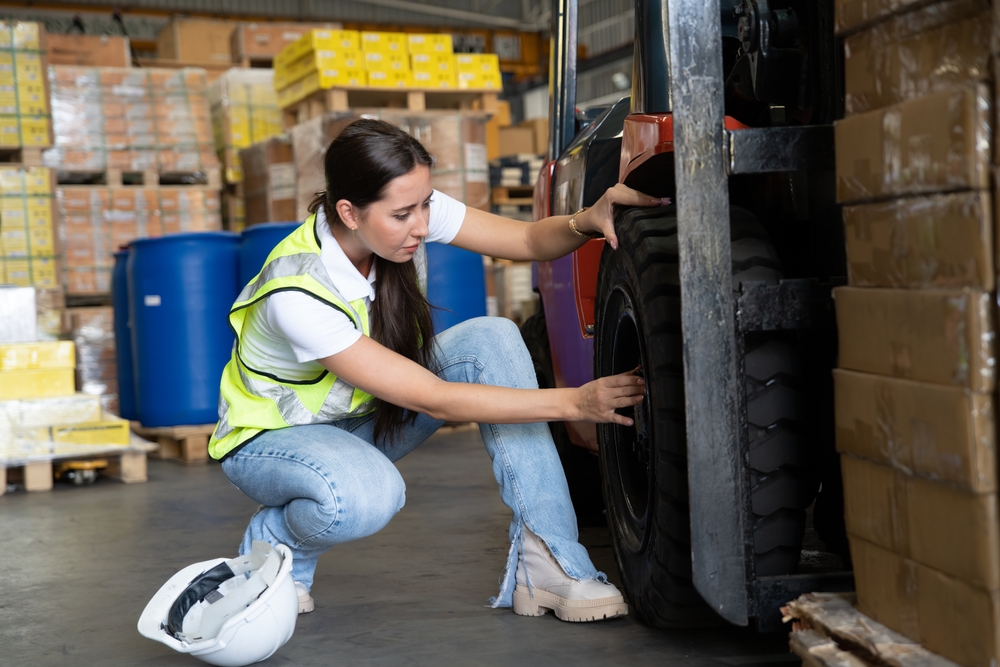
工場では設備の故障や品質不具合の流出といったトラブルが起こりやすいものです。「設備」「品質」「安全」の3つが工場で起きやすいトラブルといえるので、順に解説していきます。
設備トラブル
工場の中で一番起きやすいトラブルといえば設備トラブルです。設備トラブルになると稼働停止になるので、生産がストップしてしまいます。
24時間稼働している工場は多いものですが、常にフル回転している工場だと設備も負荷がかかるものでしょう。メンテンナンスをする時間もないので、経年による部品の摩耗や老朽化になると復旧にも時間を擁します。
また、段取りミスによるトラブルや電気系の故障もあります。このような設備系のトラブルだと、生産が止まってしまうだけでなく、すぐに復帰できない恐れがあるものです。自分たちで直せない場合は外注先に搬送して修理する必要があるため、数日間は生産が止まってしまうこともあります。
品質トラブル
昨今では自動車業界のトラブルが相次いでいますが、品質面のトラブルというのはエンドユーザーに直結するので大きな事故が懸念されます。品質面は客先からの要求もあれば、社内基準で定めた規格を満たす必要があり、これを満たさずに出荷してしまうことはあってはいけません。
品質トラブルが客先で発覚すると、苦情やクレームとなって企業の信頼性を大きく損ねる事態となってしまいます。社内で発見したトラブルもその場でしっかりと調査・対策をしていればまだしも、「このくらいならいいだろう」という安易な発想で仕事をしていると大きなクレームとなり、下手をすれば社会問題にまで発展してしまう恐れがあります。
安全面のトラブル
工場では安全第一というスローガンが有名です。設備が壊れて品質不具合が発生したとしても、人命に関わる安全が最優先されます。逆にいえば安全な職場というのは見える化ができており、品質や設備のトラブルも少ないといえます。
工場で多い事故といえば「転落・墜落」「はさまれ・巻き込まれ」です。工場勤務をしている人からすると「あるある」でしょうが、現場にはさまざまな危険が潜んでおり、ゼロにするのは至難の業といえます。
労災が発生した場合、その設備は例外なく稼働停止となります。工場長を始めとした委員会が発足し。事故防止の原因の究明が行われて暫定的な対策が取られるまでは動かせません。
ほとんどが人的要因なので、不注意や注意力の散漫からする事故は多く、人命を守るためにも早急な改善が必要といえます。
トラブルは常に潜んでいる
上記のトラブルはどれだけ注意しても起こり得るものです。機械が自動で加工しているとはいえ、その設備や搬送を段取り調整するのは作業者自身が行うものでしょう。そうなるとちょっとしたミスが思わぬトラブルを招いてしまうことが予想されます。
また、トラブルを隠そうとする傾向にある職場は、慢性的にトラブルが起きやすい状態といえます。このような職場は設備チェックシートや品質チェックの項目をレ点するだけで一切確認せず、いざトラブルが生じたときには網掛けもできないので、発覚を恐れて上長に打ち上げない可能性もあるものです。
トラブルはどのような職場でも常に潜んでいるものなので、しっかりとした対策や意識作りが必要といえるでしょう。
工場でトラブルが起きた場合の対処法
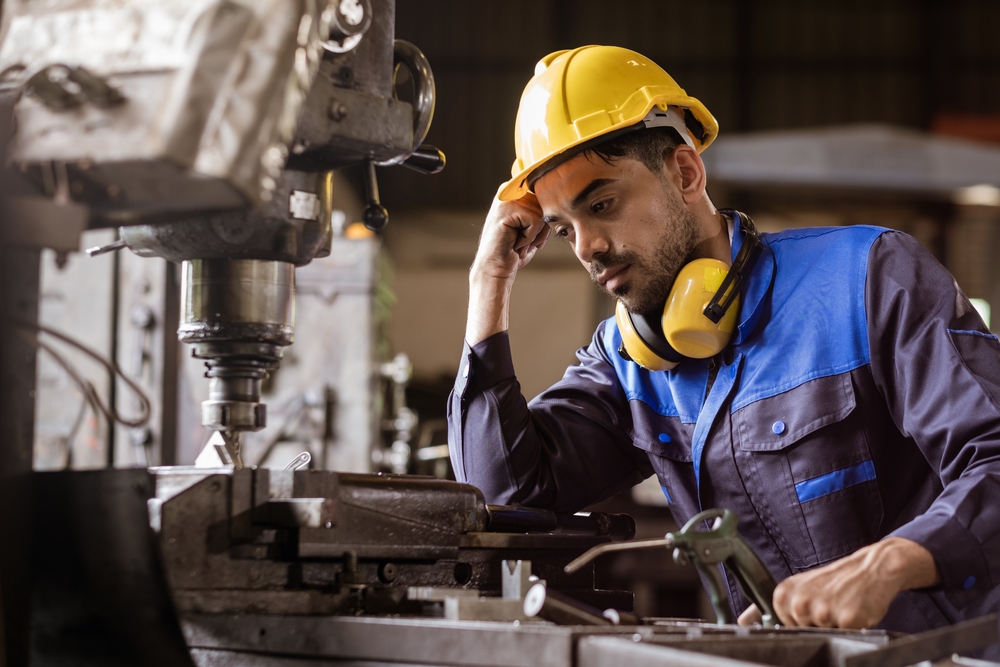
工場ではどれだけ気を付けていてもトラブルが発生してしまうものです。起きてしまったトラブルはすぐに対処しないとより重大なトラブルにまで発展してしまいます。
次に工場でトラブルが起きた場合の対処法をみていきましょう。
ケガ人の応急手当と該当ロットの出荷停止
まずは安全トラブルで作業者がケガをした場合は速やかに応急手当を施します。「意識がない」「出血が止まらない」「指を切断」などの重症時は社内で定めた応急処置のマニュアルに沿って対応し、必要とあれば救急車を要請します。日勤帯は上長や安全委員、産業医などが常駐しているので指示を仰げますが、夜間は現場の責任者もほとんどいないので迅速な行動が大切です。
設備や品質トラブルが起きたときの該当ロットの出荷や生産を停止します。現場で見つかったトラブルは網掛けといってどこで発生してどこまで浸透している可能性があるのかを見極めなくてはいけません。
トラブルが発覚した以降の工程や検査、出荷業務の該当ロットをオフラインしておき、トラブルに関与していないロットはそのまま進めていきます。
安全面のトラブルは該当設備を止めて進行しているロットはそのまま進めても問題ありません。品質トラブルは無条件で後工程を止める必要があります。設備トラブルは品質につながる恐れのある場合に限り、該当ロットをオフラインします。
トラブルが発生したら速やかに上長や関係各所へ連絡して指示を仰ぎましょう。生産がストップする場合は生産管理が生産状況を把握して計画の練り直しや客先への連絡を担います。
品質トラブルは品質保証の許可がでるまで該当ロットは動かせません。設備トラブルは生産技術が入って機械の状況を調査する必要があります。安全トラブルは職場の安全委員が調査します。
トラブルの原因究明
次にトラブルの原因究明に入ります。どのような要因によってトラブルが起きたのかという調査は今後の再発防止のためにも非常に重要です。トラブルが起きたまま放置すると、重大なトラブルにつながり、設備に至っては外注先へ修理に出すような故障につながる可能性があります。
トラブルにはなぜなぜ分析を行い、「なぜ発生したのか」を繰り返して真の要因をさがしていきます。4Mの考えから人(Man)が要因なのか、設備(Machine)が要因なのか、手段(Method)が要因なのか、材料(Material)が要因なのかを見つけて対策へとつなげていいきます。
工場でトラブルを起こさないための前対策は?
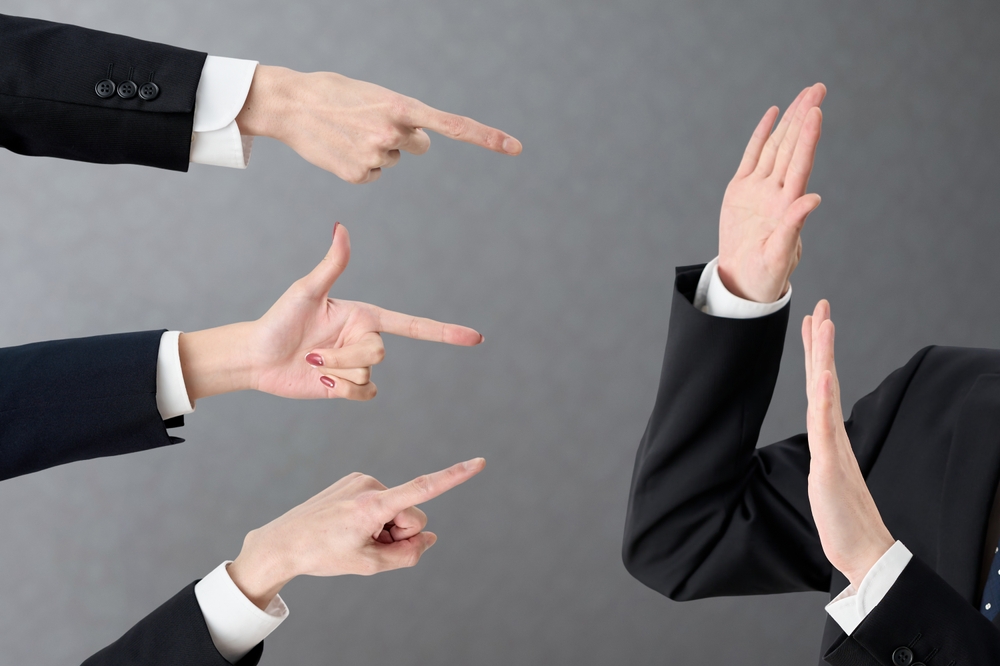
工場でのトラブルはつきものといえ、やはり事前にしっかりとした対策は必要です、どのような前対策が必要なのかみていきましょう。
トラブルを想定した職場づくり
トラブルはいつどこで起きるのか分からないので、アンテナを張り巡らしておく必要があります。トラブルが起きてから動くのではなく、トラブルが起きやすい場所を特定しておき、事前にしっかりとした対策を講じることが大切です。
トラブルの前対策できる職場づくりでは、上長に打ち上がりやすい環境や職場の見える化を推進していきます。職場の見える化には5Sの徹底が大事です。常に綺麗な状態を維持すことで普段と違う点に気付きやすくなり、トラブルの未然防止につなげることが可能となります。
予防保全・メンテナンスの定期的実施
工場の設備トラブルでは計画的な設備保全でメンテナンスを実施していくことが大切です。設備は常に稼働していますので、部品の劣化や摩耗が積み重なっていき、動作不良を引き起こす要因となってしまいます。
目で見える場所だと修理や交換が行いやすいですが、クレーンで持ち上げて本体をバラシていかないと修理できないような場合だと定期的な保全計画を練っておく必要があるでしょう。
特に同じ設備が何台もあるような職場の場合、人員に限りがあるのでまとめて保全はできません。スキルの差もあるので全員がメンテナンスを実施できるとも限らないでしょう。そこで、重保全と軽保全に分けておき、計画的な保全計画を取り入れるようにします。
現場だけで担当できる場合もあれば、生産技術が入って協業する場合もあります。保全は生産がストップしてしまうので、稼働率が落ちますから事前に生産管理と協議して生産計画に保全を入れてもらうようにしておきましょう。
計画的な保全ができるは予防保全となり、設備トラブルを早期発見できるカギとなります。大きなトラブルを避けるためにも潤滑油や作動油の補充・交換や異音の確認など、日頃の日常点検もしっかりと行いましょう。
従業員の教育・管理体制の徹底
ヒューマンエラーで起こるトラブルもあります。これには作業者の教育が重要です。ただ、教育を担当する従業員も同じ作業者だと、日ごろの生産で忙しくて教育がしっかりと行われていないこともあります。
先述した設備トラブルの日常点検もしっかりと行わないと、どのようなトラブルを誘発するか担当作業者に教育する必要性があります。「納期が厳しくて時間がない」「人手が足りない」といった理由は管理体制の問題でもあるので、上長に相談して人員の補充やヘルプ、時差稼働といった働きかけをしてみましょう。
さらに「普段トラブルが起きてないから大丈夫」といった慢心も危険です。トラブルは起きないから大丈夫ではなく、常に潜んでいるものです。ちょっとした慢心が不具合品の流出を招き、大きなクレームとなって損害賠償請求にまで発展することもあります。
安全面ではなかなか労災は起きないのでつい安心してしまい、ヘルメットをかぶらない、回転物に手を入れる、安全カバーを外して作業をするような安全面を疎かにした行動をしてしまいがちです。
これらはすべて日頃の教育や管理面体制の強化で防ぐことができます。
再発防止が風化しない取り組み
トラブルが起きてしまった場合、担当者を叱りつけるのはやめておきましょう。起こったことを掘り返しても意味がありません。原因究明のために聞き込みをするのは構いませんが、責任の所在を明らかにするために怒鳴りつけるような行為は職場のモチベーションも上がりません。
上長や先輩たちが部下や後輩を叱りつけるようになると、作業者も委縮してりまい、生産性に支障をきたすだけでなく、今後のミスやトラブルを報告せずに隠してしまう恐れがあるからです。
次につながるように再発しないようにしっかりと教育を徹底しておき、問題点を洗い出して再発防止への取り組みを実施していきます。
そのためには風化しない仕組みを作り上げ、トラブルに対しての意識を向上するようにします。
トラブル防止への仕組みづくりでは、上からの指示や命令だけでは風化しがちです。普段の作業に加えて意味のないチェックシートの増加などはもってのほかで、作業者が本当にやりやすく、意味のある内容にしなければなりません。そのためにも現場から声が上がるように意識を変えていきましょう。
ホウレンソウの徹底
トラブル防止の最善策として、現場の作業者に勝手な判断をさせないことも大切です。職場全体を巻き込んでの新しいやり方はきちんとした手順に則って行い、報告や相談を徹底してから行うようにしましょう。
本人は良かれと思って行動しても、実は品質面で規格から外れる恐れがあるやり方かもしれません。現場の声が上がりやすいように、普段からホウレンソウ(報告・連絡・相談)を徹底するようにしましょう。
横のつながりがしっかりしていると、普段と違うことに気付きやすく、トラブルを未然に防ぐことも可能です。
まとめ
工場では設備・品質・安全のトラブルが常に潜んでいます。設備は生産が止まる恐れがありますし、品質は重大なクレームになります。また、安全は人命に関わることもあるので、どのトラブルも未然に防止できるように普段か教育や管理体制を徹底しておきましょう。
また、トラブルが起きた際の対処法も、なぜなぜ分析を繰り返して真の要因から対策に移るようするのがベストです。