工場では生産性を上げていくことが大切です。品質を維持することは大前提として、生産性を向上するためにはどれだけ早く生産数を上げていけるかがカギとなります。
そのためには工場の現場をフル稼働することが重要となり、処理能力が低い設備はネック工程となってしまいます。
ボトルネックとはこの処理能力が低い工程や設備を指しており、いかに早く見つけて改善するかがポイントとなります。
そこで、ボトルネックとは何か、どうすれば見つかるのか、改善する方法も合わせて解説していきます。
ボトルネックと非ボトルネック
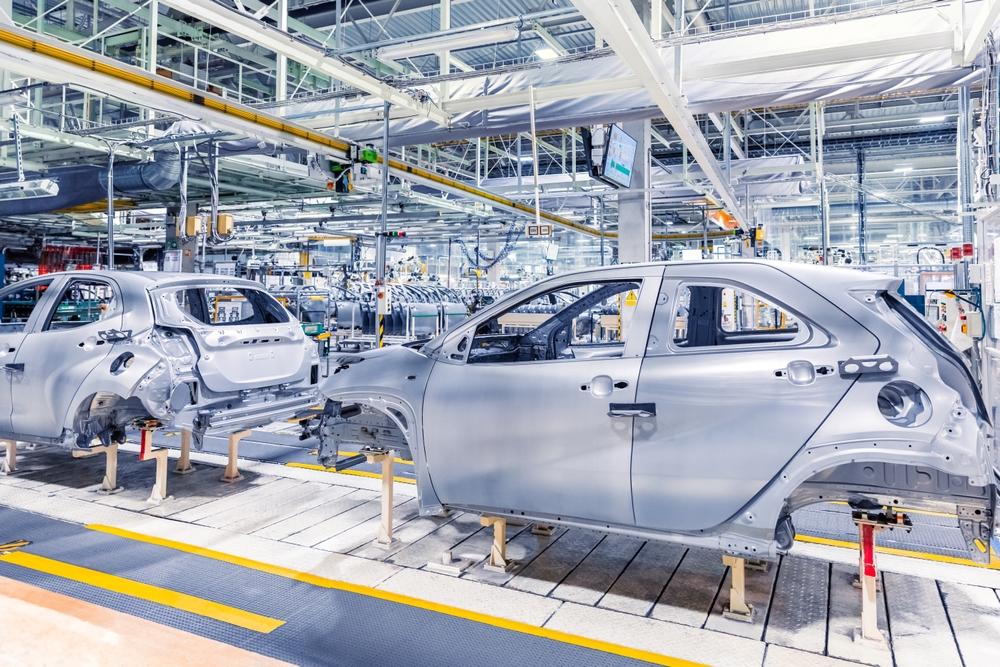
工場ではボトルネックと非ボトルネックがあります。これらを工程間の設備に置き換えてみると、簡単にいえばボトルネックは生産性が落ちて効率が悪い設備で、非ボトルネックは生産性が高く工数の少ない設備となります。
ボトルネックは中間在庫を抱えてしまう
工場では生産する工数(人・設備・材料)が少ないほど生産性が高くなります。当然ながら少ない人員で最小限の設備で、原材料も少ない中で大量生産できれば言うに越したことはありません。
製造業は生産するリードタイムが長くなればその分だけ利益が落ちてしまいます。特にさまざまな工程を必要とする場合、ボトルネックの工程があるとそこでロットが滞留してしまい、中間在庫(作り置き)が発生してしまいます。
この中間在庫は利益にならないので、早くラベルを発行して出荷しないといつまでもお金に変わりません。これらを管理するのもムダな工数であり、空いているスペースを確保して運搬する作業もムダといえます。
いってみれば処理が遅くてムダが増えているのがボトルネックです。
工数が少ない非ボトルネック
設備がフル回転してチョコ停もほとんどなく、人も少なく配置できるような設備やラインは生産性が高くなります。このような状態は非ボトルネックといえます。処理能力が高いので中間在庫が溜ることなく前工程の製品を加工することが可能です。
ただし、いくら非ボトルネックの設備が増えても、その後工程にボトルネックの設備があると中間在庫は増えてしまいます。結局在庫が溢れて非ボトルネックの設備や工程もストップせざるを得ない状況となってしまい、工場全体で稼働率が悪い状態となってしまいます。
ボトルネックの見つけ方
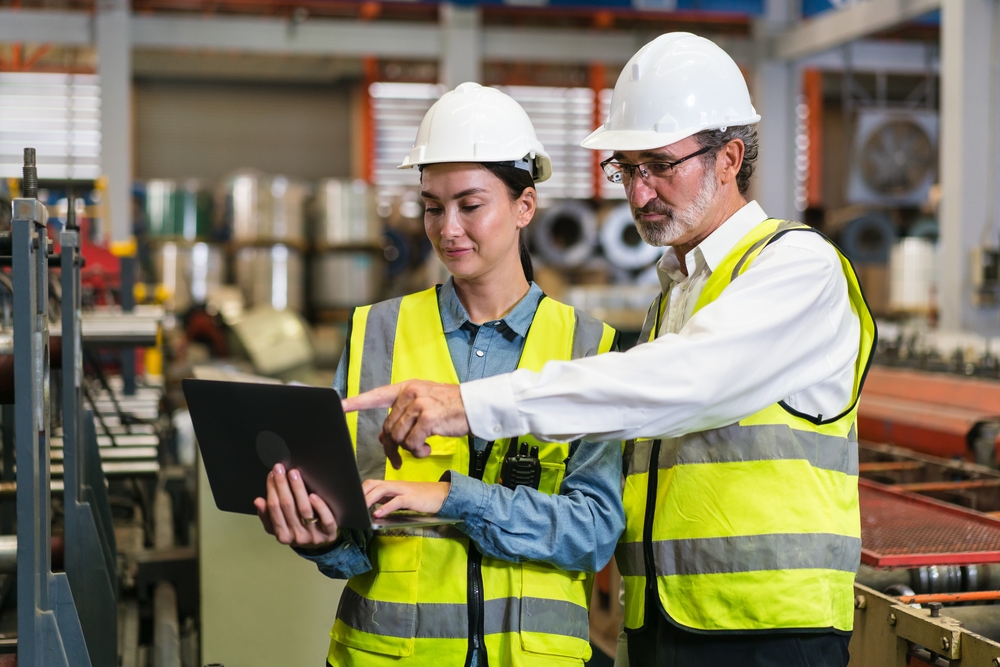
生産性向上へつなげるには、ボトルネックになっている工程を素早く見つけることが大切です。ボトルネックを早く見つける方法は下記になります。
・正しい稼働率を集計
・見える化を進める
・5S3定の維持
それでは順にみていきましょう。
正しい稼働率を集計
ボトルネックは工数が多い工程ですので、稼働率が下がっていることが考えられます。設備の稼働率は主に時間稼働率と速度稼働率があります。これらは設備から自動的に集計できるシステムがあればいいですが、多くの工場では日報から集計しているものです。
日報の生産数と設備サイクルタイムで時間稼働率が算出可能です。
・時間稼働率=(生産数×サイクルタイム÷60)÷稼働時間(分)
たとえば稼働時間が8時間(480分)、生産数が900個、サイクルタイムが20秒とする場合をみていきます。
(900×20÷60)÷480=0.625
上記の場合だと時間稼働率は62.5%となります。
ちなみに稼働した時間は300分(900×20÷60)となり、残りの時間(ダウンタイム)は180分です。このダウンタイムがどのような意味合いを持つのかで改善内容は変わってきます。
どのようなダウンタイムなのかを明確にするには、日報の内容を正確に記入しなければなりません。たとえば朝礼や昼礼、日常点検、後片付けなど毎日行う作業とは別に、不明な時間というのが浮かび上がります。作業者同士が談笑して設備が止まっているのは論外ですが、異常停止や人手が足りない場合などはきちんとした理由をダウンタイムに上げるべきです。
台風や大雪といった自然災害の影響や停電など突発的な例外は除き、設備の異常内容が同じ場合はそこを改善すれば稼働率は向上します。また、人手が足りない場合は人員配置の見直しを検討する必要があります。
工場の見える化をすすめる
ダウンタイムを正確にするには設備や工程において、何が足りないのかということを明確にするために見える化を進めます。見える化というのは、何ができていないかを抽出するためにも重要です。
たとえば段取りするのに工具が足りない、近くに置いていないということが分かるようになっていきます。
見える化ができていると、現場の作業者だけでなく、生産管理や生産技術など他のスタッフも現場の状況を把握できるようになります。ボトルネックになっている工程がどこで、どのような理由によってネック工程となっているかが見て取れますから、生産技術のフォローも早く対応することができるでしょう。
見える化によって、生産管理も計画の練り直しや他の設備でも振り回し、納期の調整などが迅速に対応可能です。
5S3定の推進
見える化を進めるには5S3定を維持していくことが重要となります。工場では品質や安全面でも重要といわれている5S3定。5Sは「整理」「整頓」「清掃」「清潔」「しつけ」、3定は「定品」「定位」「定量」です。その内容をおさらいしておきましょう。
5S
・整理…必要なモノと不要なモノを分けておく
・整頓…必要なモノを取り出しやすいようにする
・清掃…掃除して綺麗な状態にする
・清潔…綺麗な状態を維持する
・しつけ…4Sを習慣化(歯止め)する
3定
・定品…定められた製品
・定位…定められた場所
・定品…定められた量を置く
この5S3定を維持することで、工程間の設備が常に綺麗な状態となり、設備周りも不要なモノがなくなります。一番の効果はモノを探すムダがなくなることです。定位置と定量が守られていると、前工程は必要な分だけ補充することができますので、作り過ぎのムダを抑えることが可能です。
どこに何がどれだけあるのかが見て取れますので、これは現場の作業者だけでなく、他のスタッフも分かりやすいのが特徴といえます。
ボトルネックの改善
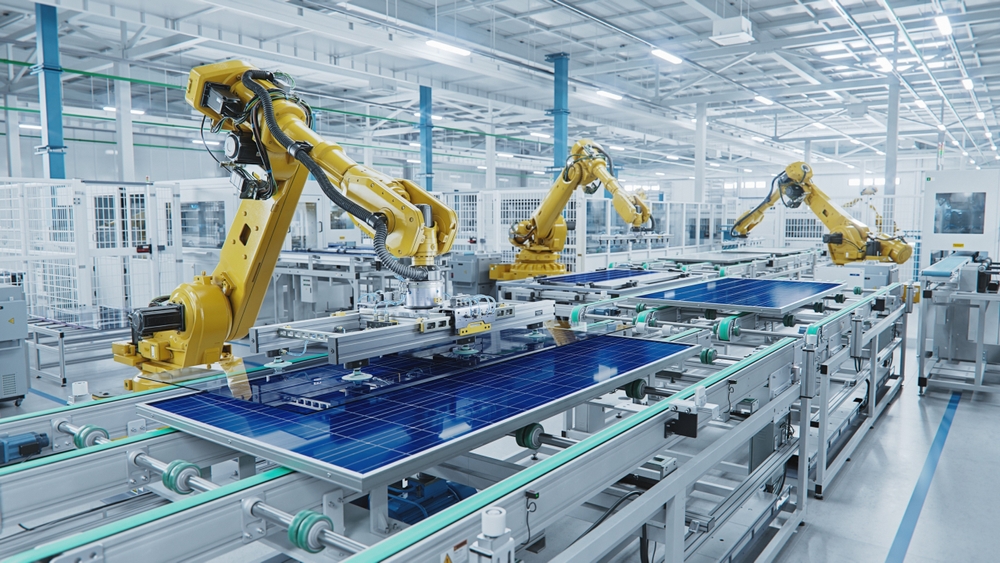
現場の見える化が進み、稼働率の集計が正確に行われるとボトルネックを見つけやすくなります。ボトルネックを改善するには工程や設備の正しい姿(あるべき姿)を再現しなければなりません。
稼働率が下がる要因として、効率の悪い加工方法やチョコ停の連発、手待ち時間の発生が主にあります。それぞれ改善方法をみていきましょう。
効率の悪い加工方法を見直す
ボトルネックの設備では作業性の悪い加工方法をしていることがあります。これは従来のやり方を受け継いでいるので、なかなか変えられない、変えようとも思いつかないといった「人」が原因の場合があります。
新しい加工方法を取り入れられない、意見ができない(通らない)などといった古い体質の職場雰囲気だと改善が進みません。特に人手不足の工場では固定した作業者が熟練者となってしまい、その人がいないと現場が回らなくなってしまいがちです。こうなると、自分のやりたいように進めてしまうので、発言力も強くなり、なかなか改善にまで協力してくれません。
稼動率をきちんと数値化して提示し、一方的に拒否するのではなく、一緒になって改善していく方法を探していきましょう。
たとえば材料の取り代が多い場合は鋼材の取り代削減を依頼することで改善できる場合があります。自工程で工数削減できれば砥石やシュー、ダイヤなどの治工具の摩耗を抑えることができるので、交換費用が抑えられて原低にも効果が期待できます。
サイクルタイムの短縮では、製品を削らない部分のエアーカットを短くすることやその部分だけ速くするなど、プログラムや加工条件の設定で見直しを図ります。
加工件以外でも作業台車の向きや高さ、積載数の増加、作業者の動線に沿ってムダな動きが多くないかというところも見ることが大切です。
チョコ停の改善
設備は大きなトラブルによるドカ停と連続作業中に異常停止が連発するチョコ停があります。設備トラブルによるドカ停は参考外といえますが、連続作業中に何度も止まるような場合はチョコ停を改善しなければなりません。
設備が止まる原因を調査し、部品の劣化や摩耗なら交換して段取りミスなら再教育を徹底するなど対策を行います。
一番悪影響なのは調査や調整に回らずに、とりあえずチョコ停と復帰作業を繰り返してその場しのぎに生産することです。これは人手が足りないという理由もありますが、作業者が調整方法を知らずに教育不足の面も懸念されます。
調整に回れないと良品や不具合品の判断も付かない恐れもあり、下手をすれば不具合品が流出することもあるので注意が必要です。
手待ち時間の削減
稼動率が低下するのは材料や人が起因する手待ち時間の場合があります。前工程の遅れによる設備停止や突発的な休みなどで人が回らないことから設備が動かせないこともあります。
前者は見える化によって工程間の進捗が追いやすくなっていきます。事前に手待ちになりそうなことが分かるので、生産管理も対策が打ちやすくなるでしょう。
後者は優先的にネック工程を動かすように意識しておき、振り回しができるようにどこの設備でも動かせる人員を作れるように教育する必要があります。
特にネック工程は重点的に人員を補充できるようにしておきましょう。
生産性向上へはボトルネックだけを見るのは間違い
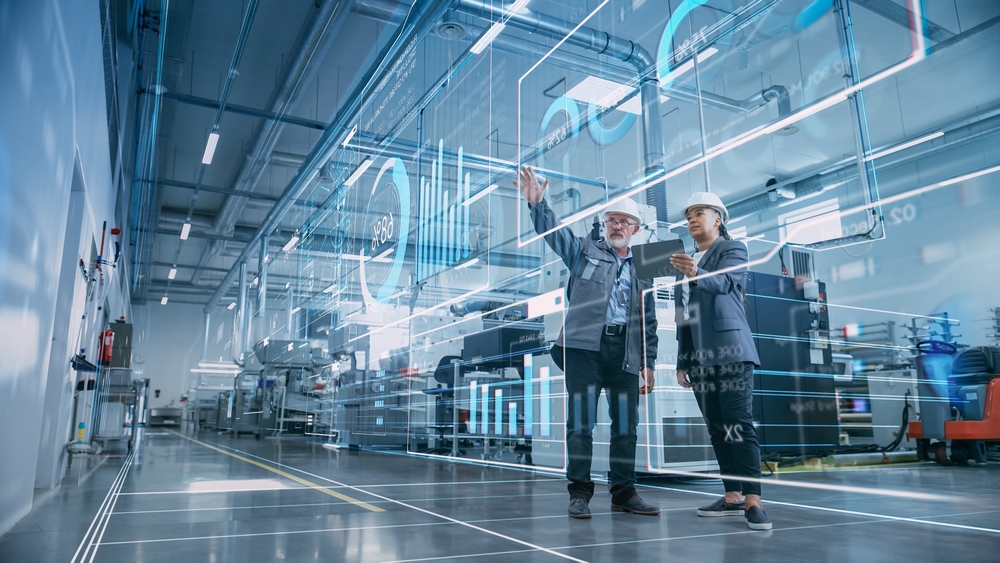
工場の生産性向上へはボトルネックに重点を置いて考えることが大切ですが、それだけでは大きな問題は解決できません。生産性の高い非ボトルネックとラインの工程間におけるボトルネックの設備との比較しておくようにもし、工場全体の流れも把握するようにしましょう。
工程間のサイクルタイムの見直し
たとえばボトルネックのサイクルタイムを改善したとします。ボトルネックで1つの製品を加工するサイクルタイムが通常20秒で、改善後に16秒まで速く加工できるようになった場合をみていきます。
|
ボトルネック設備 |
非ボトルネック設備 |
サイクルタイム |
改善前20秒 |
改善後16秒 |
12秒 |
1時間当たりの個数 |
180個 |
225個 |
300個 |
1つのサイクルタイムを4秒改善というのはかなり大きな効果でもあります。1時間当たりで45個も多く加工できますので、8時間フル稼働だと計算上は365個の差が生じるほどです。
非ボトルネック設備の工程との差を計算すると、これまでは8秒差もあったので1時間当たりでも120個から75個の差にまで減少できたので、非常に大きな改善効果にもなります。
しかし、非ボトルネック設備が後工程に当たる場合、速く加工してしまうので材料待ちとなり設備が停止してしまいます。非ボトルネック設備がどれほど材料待ちになるかはサイクルタイムから逆算できるのでみていきましょう。
・後工程の非ボトルネック設備が材料待ちで停止する時間
工程間の差(75個)=300個-225個
75個を加工する時間=75×12秒=15分
こちらを従来のサイクルタイムでも計算してみます。
|
従来 |
改善後 |
非ボトルネックの差(1h) |
120個 |
75個 |
非ボトルネックの加工時間(12秒) |
24分 |
15分 |
フル稼働時の停止時間 |
192分 |
120分 |
この15分が後工程の非ボトルネック設備の材料待ちで稼働停止になります。これが8時間フル稼働だと120分にも上り、1直の生産で2時間も停止していることが分かります。もちろん、従来の20秒で加工していた192分からは大幅に削減できるのですが、それでも1直で2時間だと夜勤もあれば1日4時間は停止していることになってしまいます。
ボトルネック設備だけを見てしまうと、このあたりに気付かないこともありますので、非ボトルネック設備と比較することは非常に重要といえます。
ただ、ベルトコンベヤーのようにラインでつながっている工程だとすぐに気付くものですが、セル生産性方式のように手ロット多品種のバッチ生産になると、他の工程と連結していないのでネック工程が改善されたと思って、全体の工程待ちがまだ解消していないのに気付くのが遅くなってしまいます。
工場全体の流れを把握する
ボトルネック設備を見つけることが重要ですが、工場全体の流れを見ることも大切です。特に非ボトルネック設備において非常に高い生産性を誇る工程があるとします。もしかすると、その工程にはスキルの高い人員を集中しているかもしれません。
設備投資を重点に行っている工程の可能性もあります。工場には係区が区切られていますが、製作課も複数存在し、その上司のパワーバランスで工場が設備に投資している金額に差が生じていることも考えられます。
設備投資の会議などは個人の作業者ではどうしようもありませんが、設備や搬送装置の導入を健闘している生産技術へのアプローチは可能でしょうし、工場全体の困りごととして訴えることもできます。
ボトルネック設備を改善するには、工場全体の流れをよく見ておき、均等に投資するお金や人を配置していくことも重要です。
もちろん、個人で動くには限界がありますので、QCサークルを活用するなどチームとして行動し、他の係区や制作課、生産技術や管理部なども巻き込んでいくと改善しやすくなっていきます。
Iotなどを活用して正確なデータを検証する
現場の作業者だと厳しいですが、生産管理や生産技術のスタッフに配属されると現場の生産性向上を外からサポートするようになります。DX化の推進などは製造業の課題として挙げられており、ボトルネック設備に稼働状況をサーバーに送信するIotのシステムを採用すると、離れた場所から現場の進捗や設備の状態を把握できるようになります。
チョコ停の異常内容の履歴、手待ち時間の詳細など、csvデータから先月との比較や他の設備との違いも分かるようになるので、原因をしっかりと検証できるようになるでしょう。
まとめ
工場の生産性を向上するにはボトルネック設備を早く見つけることが大切です。職場の見える化を進めていき、非ボトルネックとの比較をしながら改善をしていくように心がけておきましょう。