工場勤務をするにあたってよく聞くのが「トヨタ生産方式」という考え方です。製造業のトップクラスであるトヨタ自動車では、ムダを省いたトヨタ生産方式…いわゆる「かんばん方式」を取り入れています。
世界にも名だたるトヨタ自動車だけに、その影響力は凄まじく、各企業がかんばん方式を採用しているものです。
そこで、工場勤務では今さら聞けないトヨタ生産方式のかんばん方式について解説していきます。
かんばん方式とは
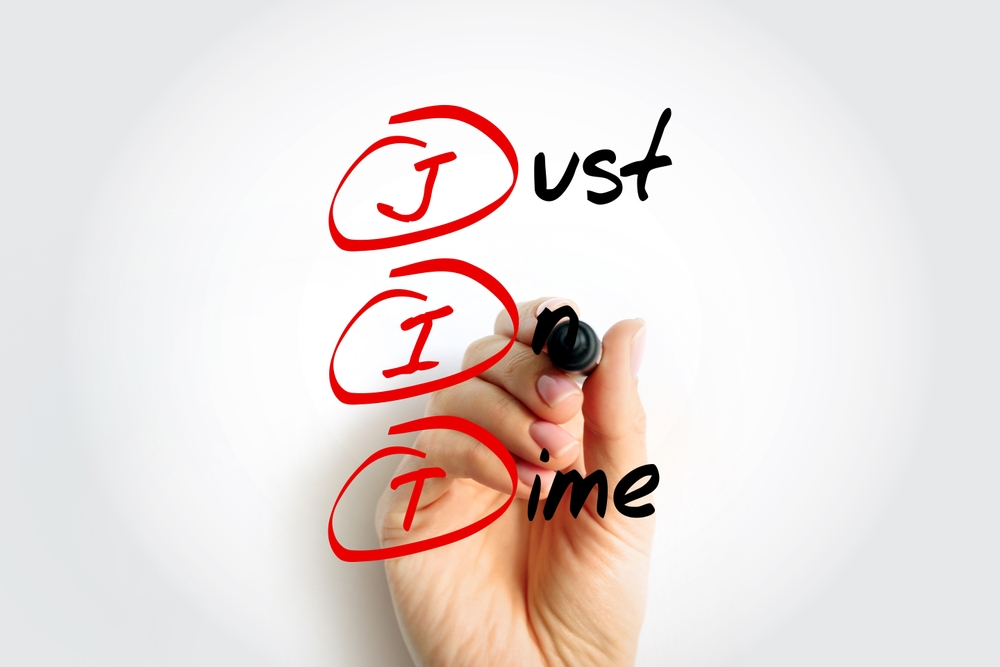
トヨタ生産方式ではジャスト・イン・タイムという、必要なモノを必要な時に必要な分だけ生産することを取り入れています。これによってムダが省かれて生産性も向上する仕組みになっています。
それを実現するのが「かんばん方式」といわれる手法です。かんばんとは生産指示書(発注書)を前工程に送り、かんばんに表示されている部品を後工程に収めるという仕組みです。
かんばんに表示されているものだけを作るので、必要な部品を必要なタイミングで必要数納品することが可能となります。工場ではさまざまな工程がありますが、どの工程でも何をどれだけ作ればいいのかが、かんばんで指示されるので分かりやすくなります。
また、前工程も必要なものだけを作るので、在庫を抱える必要がなくなります。
かんばん方式の目的
そもそも、トヨタ自動車では注文された自動車を効率よく作ることを念頭に置いており、各工程が必要な部品を作って納入することで滞りなく生産ラインを止めないですみます。これをJIT方式(ジャスト・イン・タイム)といいます。
かんばんを確認するだけで工程が円滑になりますから、工場全体の見える化にもつながり、組織として一括管理がやりやすくなります。その分だけ工程も進みやすくなり、納品もスムーズに行えることになるものです。
かんばん方式の流れ
かんばん方式は製品やロットに対してかんばんがついており、このかんばんには製品名・製番・ロット数・工程などが表記されています。このかんばんにあるロットが足りないので、前工程はかんばんの情報を見て次に何を作ればいいのかが見て取れます。
また、後工程も送られてきた製品がどの工程まで進んでどのくらい量があるのかが一目瞭然となり、運搬作業もやりやすくなって3定にもつながります。
かんばん方式のメリット
かんばん方式のメリットをみていきましょう。
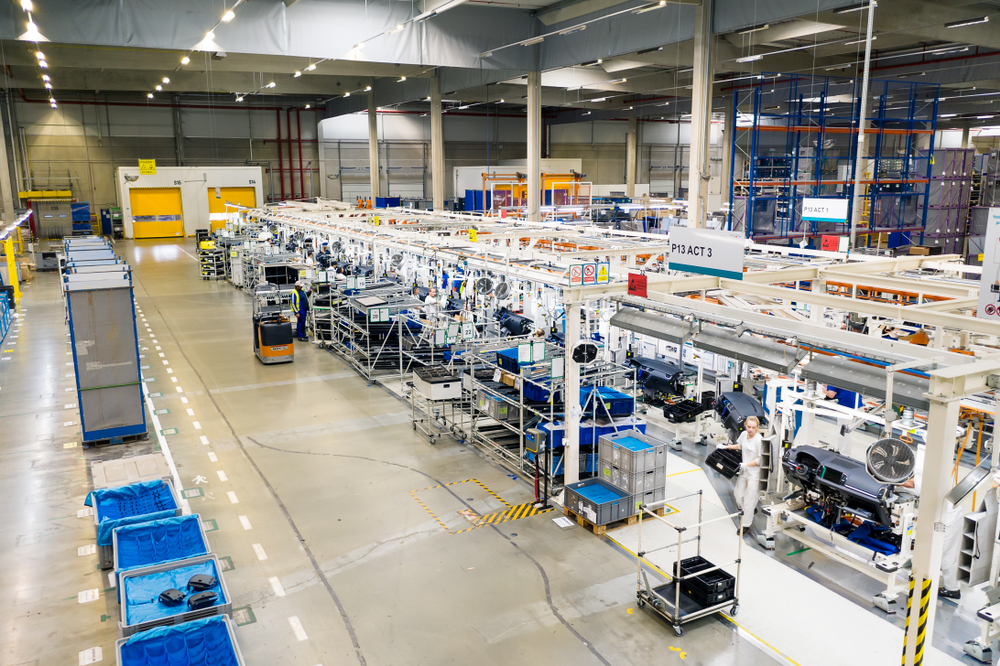
やることが明確になる
かんばん方式はやらなければならないタスクが一目で分かります。工程間のやり取りというのは、なかなか時間がかかる場合もあるものです。かんばん方式は連絡事項の削減にもなり、それだけでなく必要なことがかんばんにあるのでやるべきことが明確になります。
リードタイムも明確になっているので、いつ納品されるのかも判断しやすく、次の予定が組みやすいのが特徴です。
情報を共有できる
かんばん方式は各工程にいる作業者全員が情報を共有しやすくなります。どこの工程やラインで何が足りないのか、次に何が入るのかが分かりやすく、逆に何が出来ておらず、遅れているのかまで把握できるようになります。
生産管理や上長はもちろん、ライン上にいる末端の作業者まで情報を共有できるので、伝達事項も手短で済むでしょう。
ムダの排除が可能
トヨタ生産方式ではムダの排除を徹底しています。後述しますが、JIT方式では7つのムダの削減に取り組んでおり、ムダをなくすことで品質レベルの維持向上や納期の短縮といった生産性を高めて利益を確保する生産体制を確立していきます。
かんばん方式のデメリット
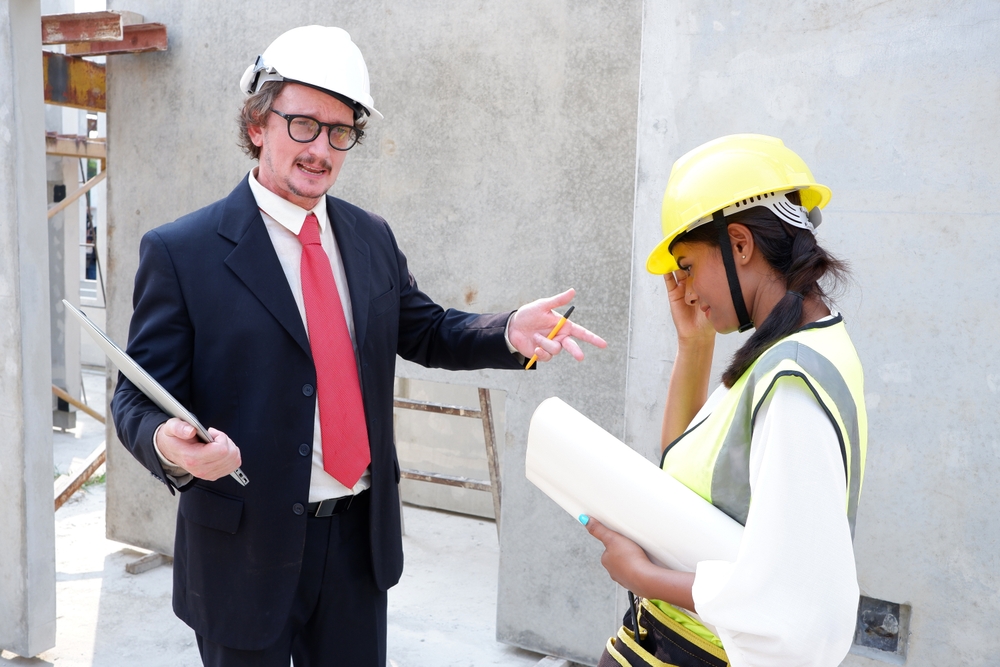
ここまでかんばん方式のメリットを説明してきました。一方でデメリットも存在しているものです。その理由をみていきましょう。
欠品が出て生産が止まるリスクがある
JIT方式では余剰在庫を持ちません。在庫を減らして必要分しか作らない仕組みを取っているからです。必要分しか作らないというのはイメージ的に効率よい仕組みに聞こえますが、万が一にもトラブルなど不具合などが発生すると、部品が足らずに欠品となってラインがストップする恐れがあります。
一つの部品だけでも欠品すると、ライン生産では工場全体に影響を及ぼす場合もあり、大きな問題につながるリスクがあります。
現場や下請けの負担が大きくなる
不良品というのは利益を圧迫するものですが、余剰在庫がないのでかんばん方式自体が不良品を出さないことが前提となっています。工場の現場ではどうしても不良品が発生するものです。
試し研削・加工で問題ないとなっても機械が誤作動を起こす可能性はゼロではありませんし、メンテナンスが必要になるケースも考えられます。
不良品を一切出さないようにするために現場の作業者に負担が強いられていることもあるのはデメリットといえます。
また、原材料から自社工場だけで一貫生産しているなら問題ないのですが、下請け工場から納品されてくる部品を扱っている場合、JIT方式だと毎日のように部品を手配しなければなりません。一か月単位での契約ならいいのですが、毎日のように納品があるとコストが増大になって下請け企業の経営を圧迫することにつながります。
物流が混乱しやすい
下請け企業の経営を圧迫することは物流にも影響してしまいます。トラックの積み荷が余裕あったとしても、取引先から要請があれば納品に動かないといけません。また、大きな工場になると複数の下請けと契約しているので、工場の周りにトラックが列をなして渋滞となり、待ち時間だけでも大きな時間の損失となってしまいがちです。
JIT方式は動かしている中心の工場では大きな効果があるものの、下請けや物流は混乱しやすくなります。
7つのムダを徹底排除
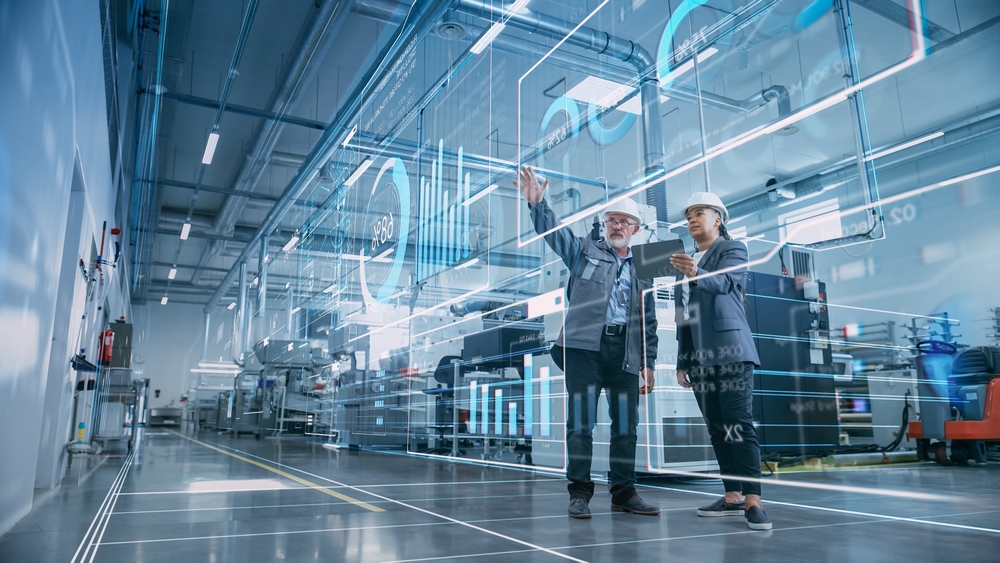
トヨタ生産方式では7つのムダを浮き彫りにして徹底排除するようにしています。
・加工のムダ
・在庫のムダ
・造り過ぎのムダ
・手待ちのムダ
・動作のムダ
・運搬のムダ
・不良・手直しのムダ
それぞれの特徴をみていきましょう。
加工のムダ
加工のムダとは、工程間の不要な作業を指しています。工場ではメインとなる製造工程から検査工程までにたくさんの人や機械が携わり、それぞれチェック項目があって次工程に流れていきます。
しかし、この工程間において実は意味がない作業も含まれているかもしれません。何となく続けていた作業や念のために行っていた作業など、根拠もなく標準書に定められていない作業を繰り返していることもあり得ます。
その作業が本当に必要なのかどうかをしっかり検証し、不要なら思い切って外すことも考えていかなくてはなりません。ただし、品質不具合が起きるかもしれないような作業は除きます。
完成品が市場に出回った場合、問題なく稼働できるための必要最小限の製造体制になっているのかどうか、しっかり確認するようにしましょう。
特に不具合が発生した場合、その対策として外観などの検査項目を増やしている場合があります。恐らく製造工程でも外観チェックをしていることが多いものですが、不具合を出さないために現場が自主的に行っている場合があります。
これは気持ち的には褒められることですが、本当の対策はそこまでチェックしなくてもいいようにカイゼンすることです。作業者のやることが増えて負担になっているのは対策ではなく、加工のムダとなります。
在庫のムダ
在庫を持つことは「念のため」というリスク回避があるからです。工場では急な発注が入った場合、在庫がないと材料を手配して特急で製造しなくてはなりません。1つか2つ程度在庫を持つならまだしも、多くのロットを抱えて完成品ラックを占拠するようなことは過剰在庫といえます。
在庫はお金に変えられません。出荷して初めて売上になります。売上にならない製品を製造していたのでは加工のムダです。さらに、在庫の管理に人手が取られますし、移動にも手間がかかります。何といっても在庫のおかげで本来一時的に保管しておきたい製品が置けないというリスクもあります。
これには生産計画の見える化やリードタイムの削減など、現場だけでなく生産管理や営業といった工場以外で各部門の協力が必要となっていきます。
造り過ぎのムダ
造り過ぎのムダとは必要以上に製造してしまうことです。これは計画に対して入荷する材料が多くなってしまい、とりあえず来月にも必要になるだろうという思い込みから現場も生産してしまうケースがみられます。
そもそも営業から注文が入って生産管理など調達係が材料の手配に動きますが、国内ならまだしも海外を取引先にしている場合、急な注文減というのもあり得ます。このようなケースは稀ですが、他に材料を振り回しできるか検討しなければなりません。
しかし、一般的な作り過ぎのムダというのは生産計画を見直す必要があり、現場との連携もできていないことがあります。
現場的には一度の段取りで大量生産できたほうが効率はいいのですが、そのおかげで他の取引先の製品が遅れるようになれば信頼を失ってしまいます。しかも、造り過ぎた製品は在庫のムダになってしまいます。
また、突発的な注文が入ったとしても、大量生産を続けていればなかなかラインを途中で止めることができません。短いサイクルで生産計画が組まれていると、突発的な注文も入れやすくなります。
手待ちのムダ
手待ちのムダとは作業者がすることがなくて生産が止まってしまうことを指しています。これは材料の手配が遅れている場合に起こりやすく、生産計画の見通しが甘いかもしれません。
生産工程におけるリードタイムの見直し、また工程間の連携の取り直しなど、自工場で出来る対策はしっかりと行う必要があります。また、工程間で設備トラブルが起きた場合にも作業者が手待ちになってしまいがちです。メンテナンスが行き届いていない場合など、トラブルで設備がストップしてしまう恐れもあるでしょう。
前工程の設備トラブルや配送時に交通事故に巻き込まれるなど、予測不能の事態が起きる場合はレアケースですが、自工場の設備トラブルがないように生産計画に保全日を組み込むなど工夫が必要といえます。
動作のムダ
製造工程においては作業者による動作のムダがあります。動作とは動き全般を表し、モノを取る・設備へ動く・しゃがむ・探すなど、多岐に渡ります。
作業者の動きは動線ともいいますが、歩数も考慮して「設備間の往復がムダではないのか」、「1つの動作で完了できないのか」など、作業者のムダな動きを探します。
段取りにおけるボルトを緩めるのに使う六角レンチやドライバーを探すのもムダになりますし、利き手によって製品を持ち替える必要がある場合なども一つの動作が繰り返しムダになるものです。
作業者は普段から当たり前の作業として携わっているので、なかなか気付きにくいものですから、第三者が入って動線を見ながら確認するのがベストといえます。
運搬のムダ
工場には運搬作業がつきものです。工程間の製品移動や検査への運搬、そして完成品の出荷までとにかく運搬作業が付いて回ります。
現場では材料の搬入から生産となりますので、工場の生産工程は運搬からはスタートするといっても過言ではありません。
ただ、この運搬作業は工場の生産工程に関して利益を生むものでありません。それでいて非常に大事な作業といえるのでムダを省くことが大事です。
納入してきた材料もすぐに使用するのなら問題ありませんが、一時保管しておかなくてはならないケースなど、生産計画とズレている場合は運搬作業のムダが発生します。後で入れ替える作業が余計に発生するからです。
また、台車やパレットの置き場が定まっていないなど、どこに運んでいいのか分からないのも作業のムダが発生してしまいます。5S3定がきっちりできていないと運搬のムダも発生しやすくなりがちです。
在庫のムダや造り過ぎのムダも運搬しなくてはなりません。運搬のムダにつながりますので、生産計画の見直しも含めて検討するようにしましょう。
不良、手直しのムダ
工場の生産では不良や手直しがどうしても発生してしまいます。不良品は廃棄処分をしますが、手直しは修理して再度品質を保つようにします。これまでの工程がムダになってしまいますので、特に力を入れたいところでしょう。
なぜなら、これまでのムダに関しては最終的に売り上げに直結します。しかし、不良品は廃棄すればお金になりませんし、手直しも工程をやり直すことになるので余分なコストが生じてしまいます。
また、不良品も重大クレームにつながりそうな場合は原因・対策をしっかりと講じる必要があり、生産ラインがストップする可能性もあります。特に選別作業が入って良品と不良品を分ける場合には人手も要りますし、納期に間に合わないケースもあるでしょう。
多大な影響を及ぼしてしまうのが不良・手直しといえます。しかし、この不良や手直しが減れば、その分だけ売上につながりますので、対策を講じる価値は十分あるといえるでしょう。
ムダを省いてカイゼンにつながる
ここまで紹介してきた7つのムダを省いていけば、カイゼンにつながって利益確保にもなっていきます。かんばん方式は工場のムダを徹底的に省く要素がありますので、まずは7つのムダをチェックすることから始めてみましょう。
作業のムダがなくなっていけば、作業者も働きやすくなり、モチベーションも向上していきます。生産計画が順調に進めば、これまで設備がストップしていた時間がなくなっていきますので、浮いた時間を設備のメンテナンスや人材教育に回すことも可能です。
このようにカイゼンが進めば働きやすい職場となって、工場全体の組織力が上がることでしょう。
まとめ
トヨタ生産方式では製造工程における7つのムダを省いて生産性を向上させています。その手法として、工場でかんばん方式を採用しているのです。
自社工場に適した手法かは分かりませんが、ムダを省く要素は工場勤務の知識として持っておくと便利といえるでしょう。